Swarf processing
The basic facilities in this area are:
- Segment or shaft chip crushers
- Chip centrifuges
- Briquetting presses
- Regeneration of cutting fluids
- Chip conveyors
- Drum metal chip separators
- Chip trolleys
- Pallet hoppers
From our range of high-performance equipment and individual components, we configure chip management suitable for every production or processing environment. The equipment supplied by us can be easily integrated into existing processes and allows you to choose the appropriate format for the final product.
Crushers
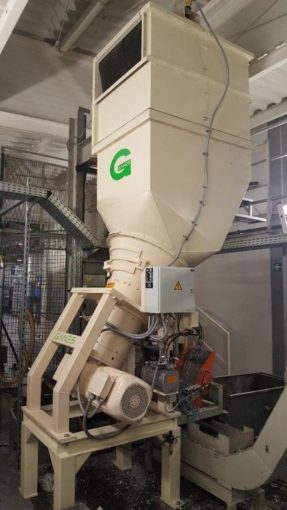
RS series segment type
Throughput: up to approx. 8 t/h (steel) depending on material and chip form
Drive: electric or hydraulic (higher power)
Large pieces and rod ends initiate blockage control and ejection. For pieces larger than the ejector opening, the crusher is automatically switched off without any damage. The piece can then be removed manually through the inspection opening.
By means of a hydraulically or pneumatically operated turnout, the piece parts are diverted away from the chips.
ZW series shaft type
Throughput: up to approx. 3 t/h (steel) depending on material and chip form
Drive: electric
Design: single-shaft, double-shaft
Large pieces and rod ends initiate blockage of the crusher. They must then be removed manually through the inspection opening.
Optionally, the crusher can be equipped with a replaceable screen with optional perforation of the holes influencing the final size of the crushed chips.
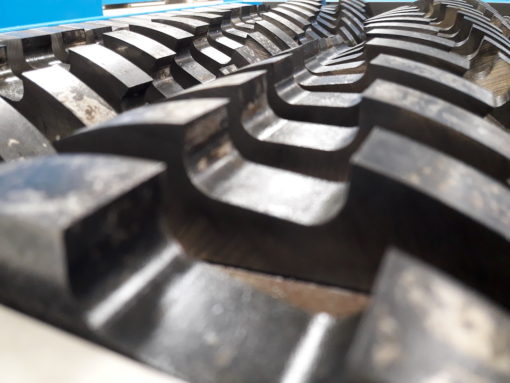
Centrifuges
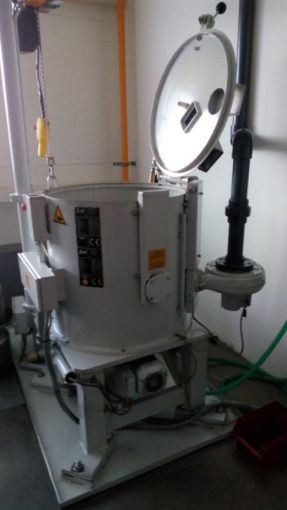
Industrial centrifuges
According to the purpose of use (de-oiling, drying, washing, rinsing, coating) and design (manual, automatic) centrifuges are marked as follows:
Polar C – for manual operation, charge up to 300kg (200 dm3), max. 10 charges/h
Polar F – for manual operation, charge up to 300kg (200 dm3), max. 25 charges/h
Polar Z – special design for hot dip galvanizing
Polar FK – tilting centrifuge, charge up to 300kg (70 dm3)
Polar K – continuous automatic centrifuge, throughput up to 10m3
Polar E – batch automatic centrifuge, charge up to 300kg (120dm3), max. 10 charges/h
Chip conveyors
General information
Processing of metal chips requires their movement through the space, either towards the processing equipment (crushers, centrifuges, presses) or between individual components of technological lines.
This function can be performed by different types of conveyors (chain, harpoon, worm, vibrating, magnetic, etc.) or by piping system (vacuum or liquid).
In its facilities, our company applies and delivers conveyors of mostly rake and sectional design.
According to necessary transport capacities and distances, the standard dimensions of the cabinet width are 300, 500 and 800 mm with a length of up to approx. 25,000 mm.
The transported metal material is considerably abrasive, and therefore the construction and design of the conveyors is adapted to this fact – the use of abrasion-resistant materials on stressed surfaces and high-quality link chains is a matter of course.
Where the technical solution requires it (hoppers, dispensers), our delivery includes worm or vibration conveyor versions.
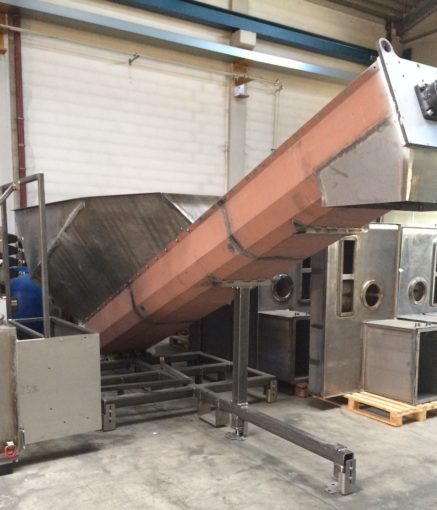
Centrifugal cleaning of liquid
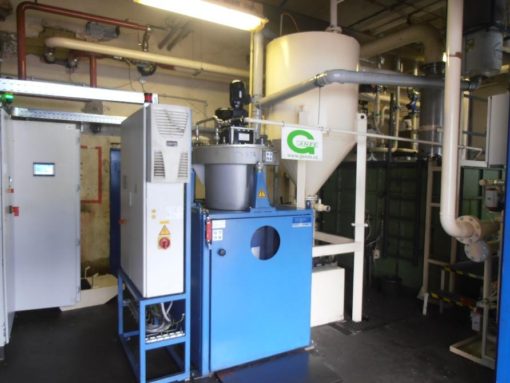
General information
- oil cleaning
- removal of abraded material and oils from emulsions
- cleaning of cooling water used in glass grinding
- separation of liquids of different densities
For this equipment we offer:
- Centrifugal separators with manual discharge of sludge fraction
- Centrifugal separators with automatic sludge fraction discharge
- Achievable separation of these devices is up to 5μm and flow rate up to 150l/min.
Drum metal chip separators
General information
Metal chip processing requires maximum separation from lump admixtures.
This function can be provided by different types of separators (vibrating, finger, drum, magnetic, etc.)
In our facilities, our company applies and delivers mostly drum and vibrating separators.
According to the required transport capacities and distances, standard dimensions of drums are 400, 500 and 1,000 mm with a length of up to approx. 3,000 mm.
The transported metal material is considerably abrasive, and therefore the separator construction and design is adapted to this fact – the use of abrasion-resistant materials on stressed surfaces is a matter of course.
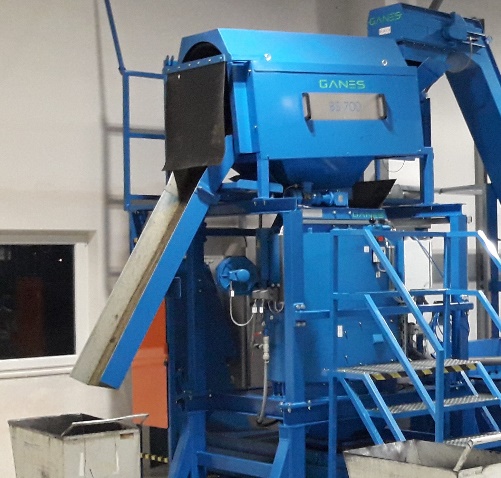
Chip management
Download the catalogue in PDF.